Global Machine Market supplies molds for any of the block, press and forming machine on the market today.

Wide variety of molds can be made for most any concrete product. We make molds and mold parts for Besser, Columbia and foreign paving stone and block machines.
As a third generation equipment builder my family started making molds for our own machinery in 1943. Global Machine Market offers molds a wide range of USA building block machine makers such as Besser and Columbia and foreign paving stone and block machines. We use the same experience we have gained for 7 decades and make molds for any block and paving stone machine. Give us a call with your specific mold request at 314-960-0540.
A mold is required for every specific shape and size product you want to make in a block, paving stone or press machine. A conventional building block mold made for USA machine consist of two parts. An upper section caller the plungers or some call the press head and the lower section called the mold box or insert section.
The mold box is normally manufactured in two different methods depending on the type of product you are wanting to produce. When making building blocks in the USA we only manufacture and supply bolt-in replaceable designed molds and mold parts. The advantage of this design is when the internal parts wear outside the acceptable product tolerances only those individual internal parts need to be replaced in the mold.
The other method which is widely accepted in other parts of the world is called a one piece version mold which is an all welded construction where the inner wear liners and frame of mold are welded together as one unit. When one cavity wears past the acceptable product tolerance the producer has to invest in labor intensive welding repairs. This can lead to weakening the life of the mold due to welding which effects the inner hardness and cycle life of the mold. The only other option is to replace the entire mold. Both methods make an accurate and dimensionally correct concrete product if made correctly. A welded design mold is normally more affordable in the beginning purchase price compared to a bolt-in replaceable design. However in the long term a bolt together mold is almost always more cost efficient with more long term advantages. Advantages and disadvantages of each design depend on many aspects. Some of the dynamics that need to be considered would be the amount of product volume you what to produce, your budget, delivery times, type of machine you are producing products on and the height of the product be produced.
The lower section of the molds consist of an outer mold box containing several bolt-in replaceable mold wear liners. The liners determine the outer shape of the block while the inner liner shapes of the other side of the block. As many as 15 building blocks may be molded at one time.
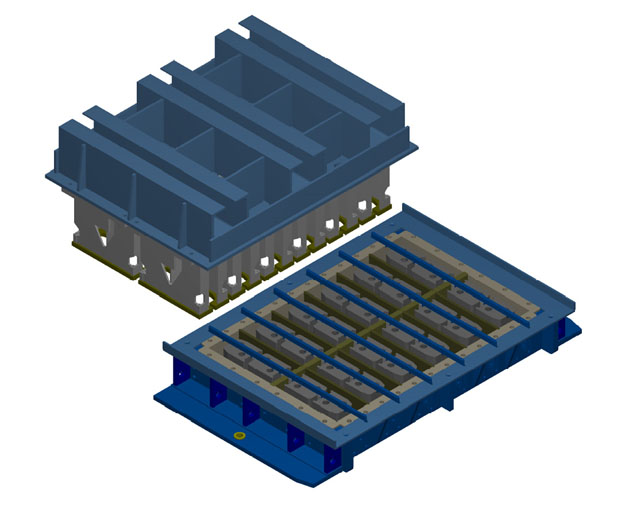
Once the lower mold cavities are full of concrete the second upper press head or plungers section of the upper mold lowers into open cavities of the mold box. Sometimes the plungers are assisted into the cavities by hydraulic pressure and other times by just gravity depending on the type of block or paving stone machine you operate.
Once the compaction head is in the mold box the vibration of the mold is occurring at the same time and the proper height and density of block or paving stone unit is achieved. The concrete products are then demolded leaving the concrete products onto a production pallet and the pallets are taken to a curing area. The same process with the mold is repeated again for thousands of times in a typical day. With some of the high production block machines this molding process can take only 6.5 seconds.
www.Bessermakingblocks.com video jing
A paving stone mold is very similar in the design and also has two main sections to the mold. Commonly in the industry they refer to the upper section as the tamper head or press head and the lower part of the mold as the insert section or mold box. Bolted onto the tamper head are replaceable tamper press plates which is what makes contact with the concrete material when lowered into the mold cavity.
The major difference is typically the bottom sections of the inner mold or what is called the mold insert were only flame cut until the early1980’s. I am proud to say my company was one of the first companies to start the process of offering the technology to supply the machined insert sections as an option for large pallet machines. This allows paver producers to have an insert that any press plate could fit any cavity. More important the life cycle of the mold increased dramatically by being able to carbonize the insert and tamper shoes to a greater depth than what was previously being achieved by flame cutting technology. Although a machined mold initially more expensive as a first purchase over a short period of time it pays for insert very quickly in just longer lasting cycles along with many other benefits. The producer also gains the advantage of every cavity is exactly the same and no more had fitting molds which was a common negative to flame cutting technology.
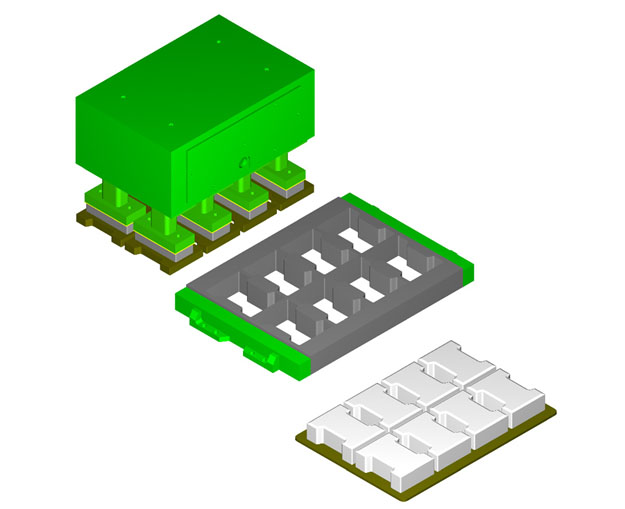
Illustration of upper section (tamper head or press head) & lower (insert section or mold box). Pavers on pallet.
- What makes our molds unique over some of the molds manufactures in the world is we use the most up to date software programs available to draw molds. Using CAM Software for automatic 3D milling guarantees you will have high quality parts in a timely manner.
- When it comes to paving stone molds for Besser and Columbia building block machines we only use the best grade of USA steel and heat treated to provide long lasting longevity. Another important value is all our Paving Stone molds are machined from a solid piece of steel using CNC machining centers. This provides the Besser and Columbia block machine owners a much longer paving stone mold life than the old technology of flame cutting molds.
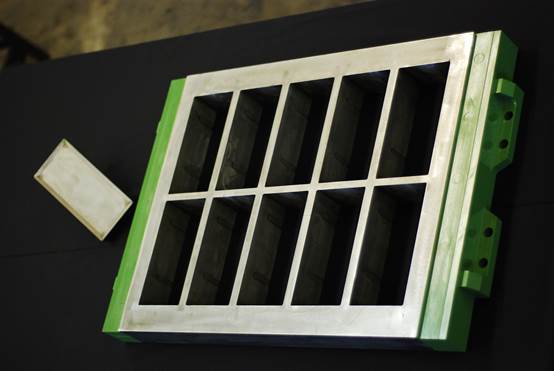
Columbia Block Machine Paving stone molds are all CNC machined & heat treated for long mold life.
- Our molds are made in North America.
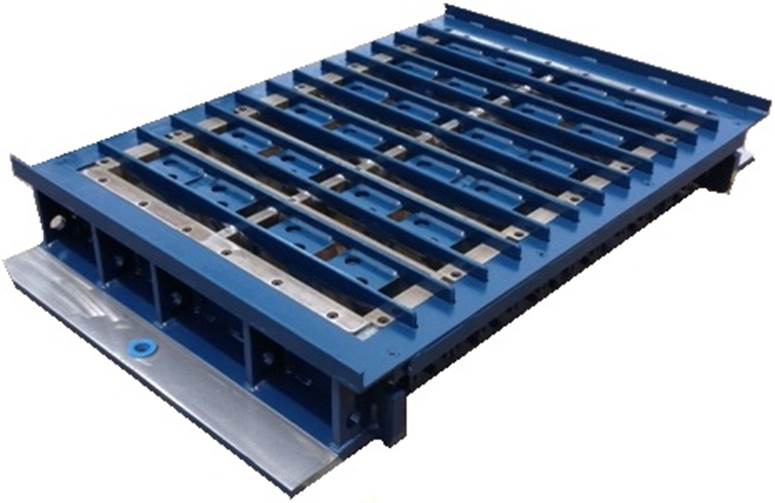
Hess RH2000 Bolt-In Replaceable Building Block Mold. USA made with heat treated parts for long lasting wear and USA service.
- We stock bolt-in replaceable building parts for USA made for Columbia and Besser building block machines.
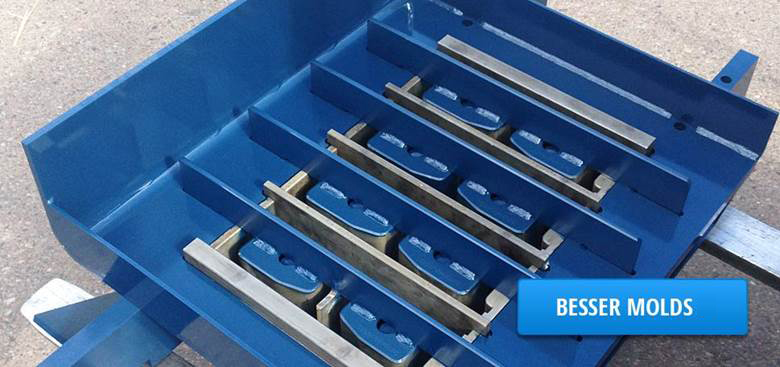
Besser V312 Building Block 6”x6”x18” Mold above. We stock Besser & Columbia block machine bolt-in replaceable mold parts.
- High quality steel is used to manufacture the molds. We use unique heat treating process to allow molds and wear parts to last longer saving you money is gaining longer mold life.
- The Fleming family has been building molds since 1943 for concrete block machines. With today’s state-of-the-art CNC machines, heat treating technics, 3-D CAD systems, prototyping and scanning, today molds are better quality and more versatile than ever. You can actually create your own unique slab or paving stone surface.
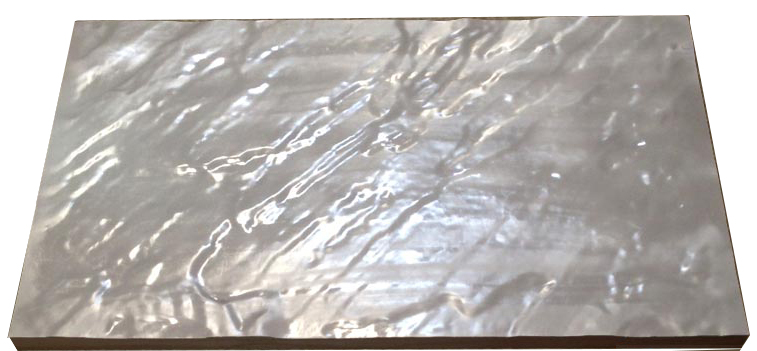
We Offer custom machined textured shoes for any concrete paving & building block machine for your paver and decorative molds.
- If you can supply me a sketch, photo with dimensions we can have it drawn professionally to show you how many units you would make in a particular sized machine mold. We also have 3 D modeling programs to assist you in creating your products for manufacturing your dreams into reality. After you see the drawings you can change any details and we can re-edit your changed to meet your needs. We then will be able to provide you an accurate price investment for your new concrete block, paving stone or retaining block mold.
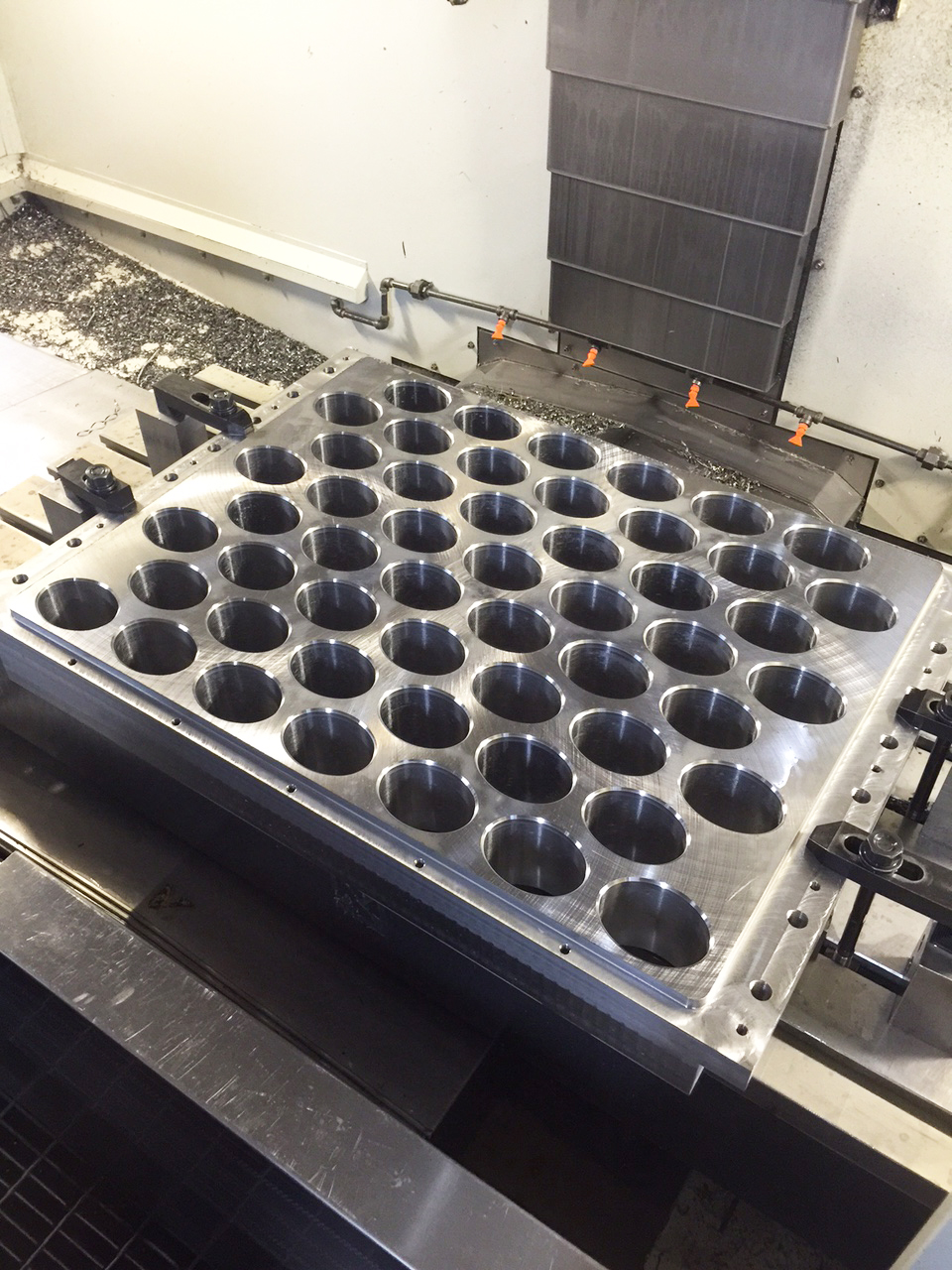
We build custom molds for Besser & Columbia block making machines with just a dimensional sketch from the producer. Above is machined insert being made for paving stone mold.